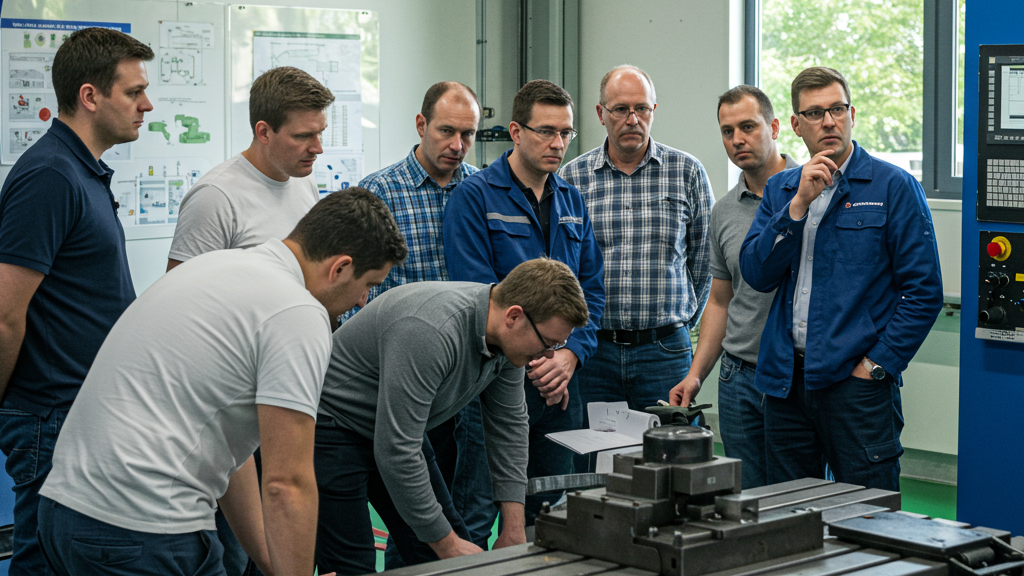
In modern manufacturing, injection molding technology is widely used because of its efficiency, precision, and cost-effectiveness. To ensure the quality and consistency of injection molded products, process stability is crucial.
The stability of the injection molding process does not happen overnight, and it requires precise control and optimization of several critical steps. In this article, we will take a closer look at the core factors that affect the stability of the injection molding process and explain in detail the key steps to achieve stable production.
Raw Materials vs. Molds: How Does Stability Affect?
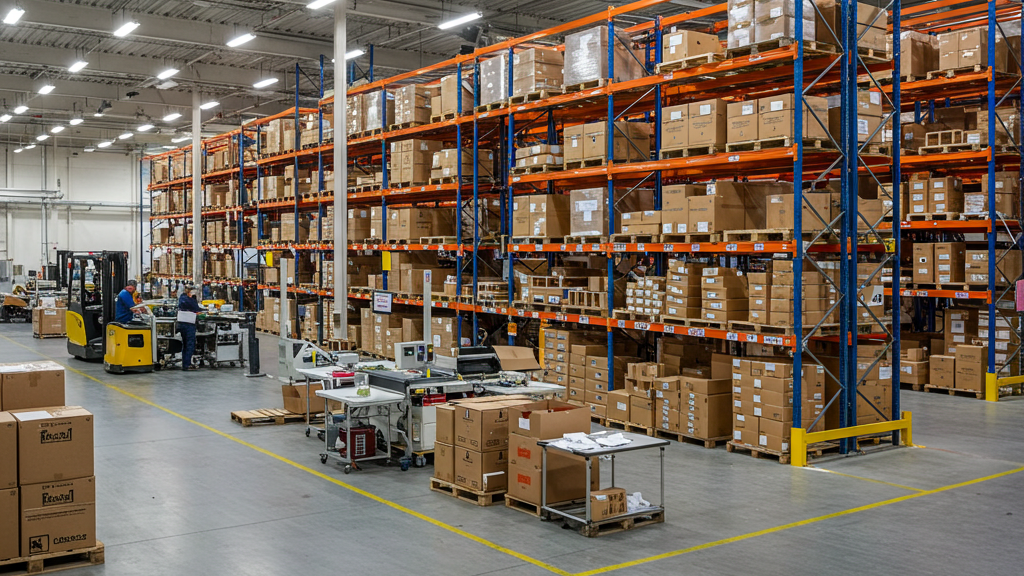
In the injection molding process, high-quality raw materials and well-designed molds are the basis for the stability of the injection molding process. By strictly controlling the quality of raw materials and strengthening mold maintenance, the stability and consistency of products can be effectively improved.
- Consistency in raw material quality: High-quality and consistent raw materials are the basis for ensuring the stability of product size and appearance.
- Pre-treatment of raw materials: Correct pre-treatment of raw materials, such as drying, can effectively avoid product defects.
- Rationality of mold design: Reasonable mold design can ensure that the molten plastic is evenly filled and reduce product deformation.
- Mold maintenance and maintenance: Regular maintenance of the mold can prevent defects in the product and ensure that it is in good working condition.
Injection Molding Machine Parameters: How to Ensure Stability?
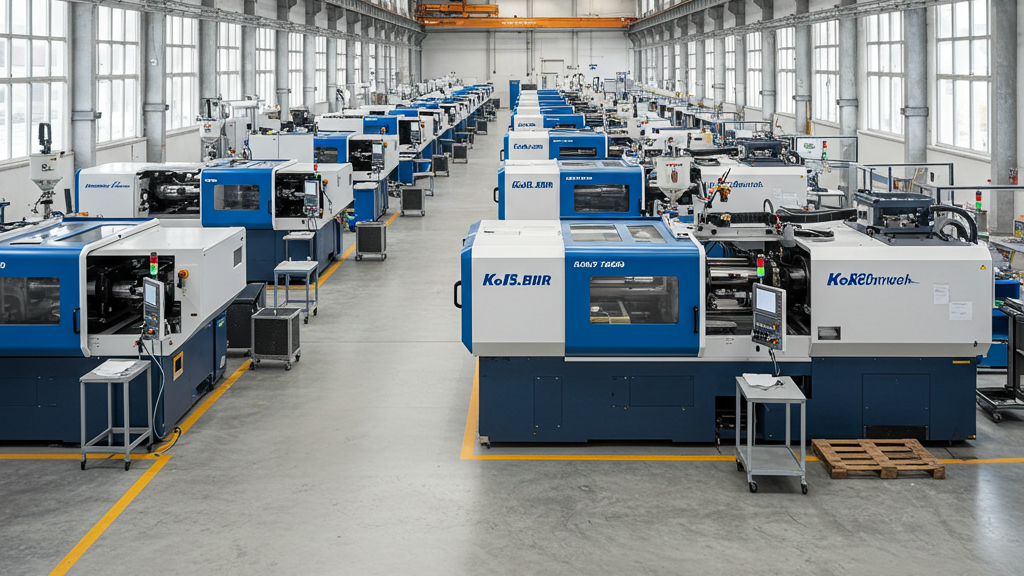
In the injection molding process, the stability of the injection molding machine parameters is the core to ensure the consistency of product quality. Ensure the stability of the parameters of the injection molding machine, so as to improve the quality and production efficiency of the product.
- Precise temperature control: Whether it’s a barrel or a mold, keeping the temperature stable is key to ensuring the flow of molten plastics and the quality of their products.
- Stable adjustment of pressure: Precise control of injection pressure and holding pressure can ensure that the plastic fills the mold cavity fully and prevents product defects.
- Reasonable setting of speed: Proper adjustment of injection speed and screw speed can avoid the problem of unstable flow and uneven plasticization.
- Regular maintenance and monitoring of equipment: Through regular maintenance and real-time monitoring, the stability and accuracy of various parameters of the injection molding machine are ensured.
Quality Control & Optimization: How to Do It Effectively?
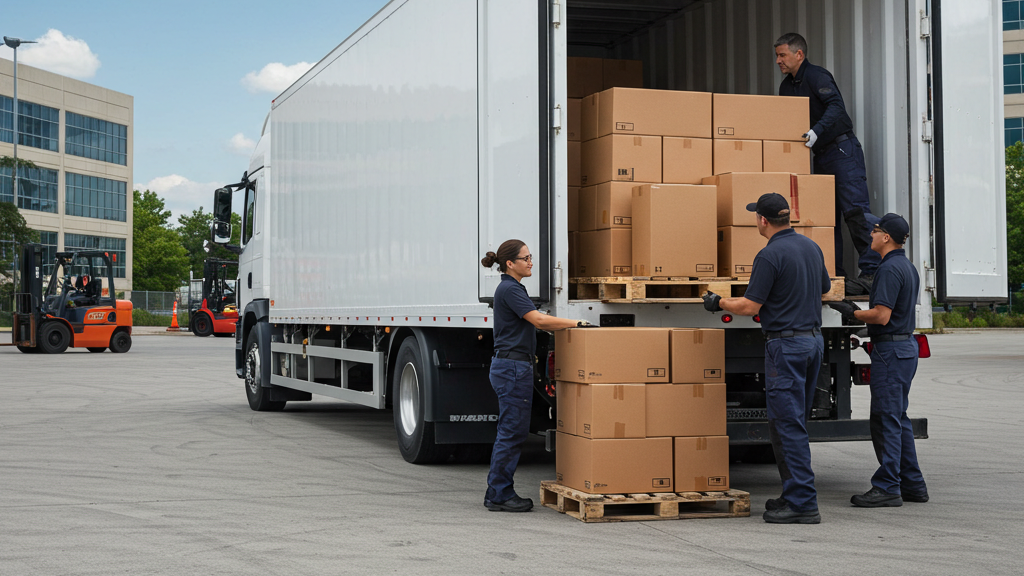
In injection molding production, we must attach great importance to quality control and optimization, which runs through all aspects of production to achieve excellent quality and efficient production of products.
- Establish a sound quality control system: ensure that products meet quality requirements through standard formulation, process monitoring, inspection and testing, and data analysis.
- Implement continuous process optimization: Continuously improve production efficiency and quality through optimization of process parameters, tooling and equipment, as well as personnel training.
- Use scientific management methods: use statistical process control, Six Sigma and lean production methods to continuously improve the production process.
- Establish a feedback mechanism: through customer and internal feedback, understand and solve problems in a timely manner, and continuously improve products and processes.
Injection molding production process traceability table
Production stage |
Critical control nodes |
Examples of core parameters |
Common problems and solutions |
Raw material handling | The material dries | Temperature: 80-90°C (ABS), Time: ≥2 hours | Bubbles/Silver Grain → Raise the drying temperature or time |
Injection molding | Melt filling | Injection pressure: 60-150MPa, V/P switching point: 95% cavity filling | Short shot → to increase the pressure or adjust the switching point |
Packing pressure cooling | Holding pressure control | Holding pressure: injection pressure 50-80%, cooling time: wall thickness×2 times | Sink marks → Extend the dwell time or increase the pressure |
Demoulding inspection | Product demoulding | Ejection speed: 10-30mm/s, mold temperature: 40-80°C | Top white/deformation → Optimize ejection balance or mold temperature |
Use technology to ensure process stability
In modern injection molding production, technology has become the core driving force for ensuring process stability. The comprehensive application of technology not only improves production efficiency but also significantly reduces scrap rates, providing a solid technical guarantee for achieving high-quality, high-efficiency injection molding production.
1.Automation and Intelligent Control Systems: Through real-time monitoring and data analysis, achieve automatic adjustment and optimization of process parameters.
2.Precision Equipment and Mold Technology: High-precision equipment and intelligent molds ensure production accuracy and stability.
3.Digitalization and Simulation Technology: Utilize simulation software and digital management to optimize process design and production traceability.
4.Quality Detection Technology: Online and non-destructive testing technologies ensure the continuous stability of product quality.
conclusion
In summary, the stability of the injection molding process is crucial for ensuring product quality and production efficiency. By strictly controlling and optimizing raw materials, molds, injection molding machine parameters, production environment, and quality control, we can improve the stability of the injection molding process.
For expert assistance in implementing for your production needs, visit our resource center or contact us. Let’s help you scale up your manufacturing with precision and efficiency!
Post time: Mar-07-2025